Arang dikemas dalam karung @25 kg dan siap diangkut dengan dokumen-dokumen yang sah.
Senin, 03 November 2008
Pembukaan Tungku Arang Pertama
Arang dikemas dalam karung @25 kg dan siap diangkut dengan dokumen-dokumen yang sah.
Jumat, 10 Oktober 2008
Charcoal Briquette


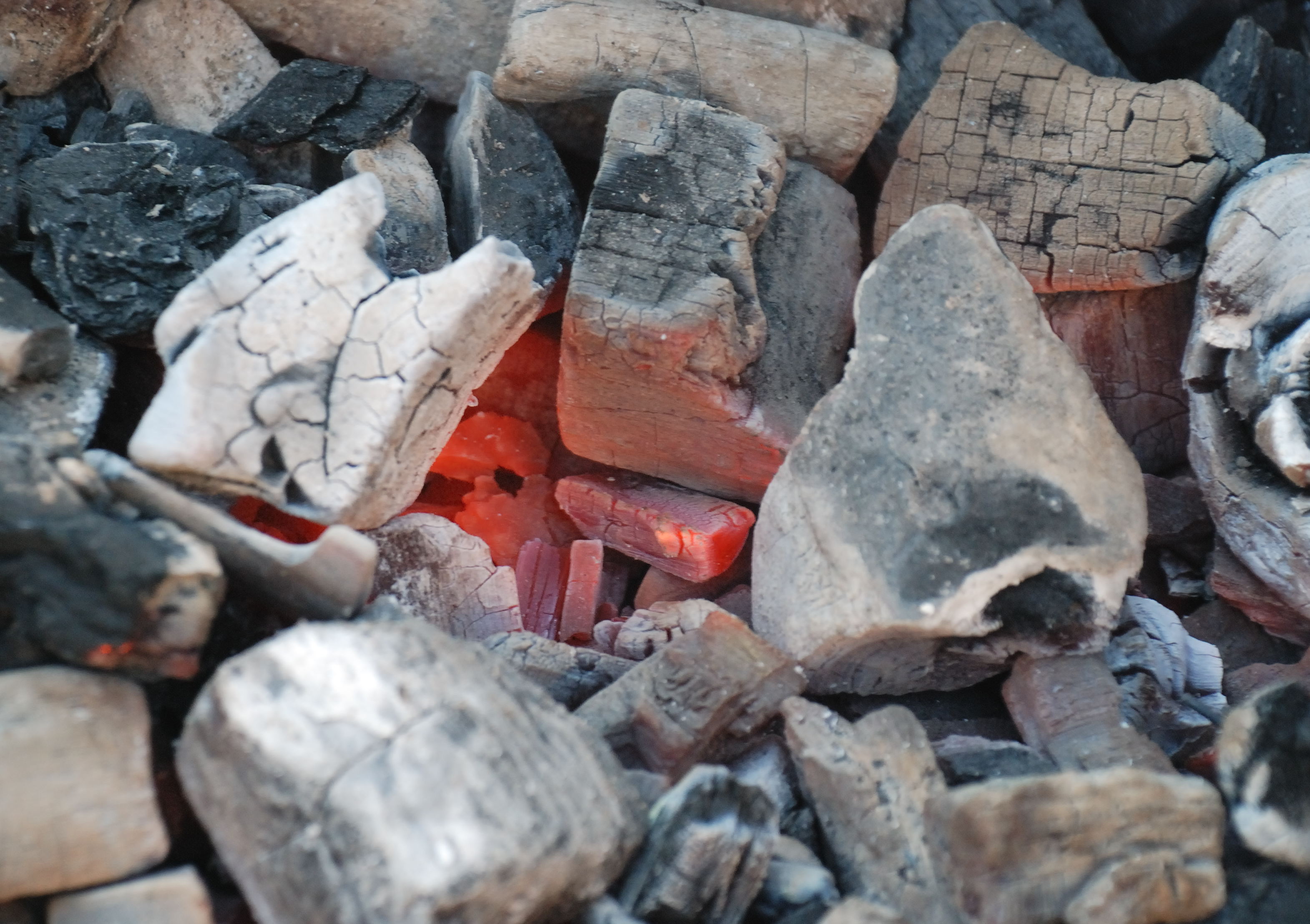
Charcoal burning
Charcoal is the blackish residue consisting of impure carbon obtained by removing water and other volatile constituents from animal and vegetation substances. Charcoal is usually produced by heating wood, sugar, bone char, or others substances in the absence of oxygen (see char). The soft, brittle, lightweight, black, porous material resembles coal and is 85% to 98% carbon with the remainder consisting of volatile chemicals and ash.
The first part of the word is of obscure origin, but the first use of the term "coal" in English was as a reference to charcoal. In this compound term, the prefix "chare-" meant "turn," with the literal meaning being "to turn to coal." The independent use of "char," meaning to scorch, to reduce to carbon, is comparatively recent and must be a back-formation from the earlier charcoal. It may be a use of the word charren or churn, meaning to turn, i.e. wood changed or turned to coal, or it may be from the French
charbon. A person who manufactured charcoal was formerly known as a collier, though the term was used later for those who dealt in coal, and the ships that transported it.
Wood pile before covering it by turf or soil, and firing it (around 1890)
An abandoned charcoal kiln near Walker, Arizona.
Modern charcoal retorts
Production of wood charcoal in districts where there is an abundance of wood dates back to a very remote period, and generally consists of piling billets of wood on their ends so as to form a conical pile, openings being left at the bottom to admit air, with a central shaft to serve as a flue. The whole pile is covered with turf or moistened clay. The firing is begun at the bottom of the flue, and gradually spreads outwards and upwards. The success of the operation depends upon the rate of the combustion. Under average conditions, 100 parts of wood yield about 60 parts by volume, or 25 parts by weight, of charcoal; small scale production on the spot often yields only about 50%, large scale was efficient to about 90% even by the 17th century. The operation is so delicate that it was generally left to professional charcoal burners. These often worked in solitary groups in the woods and had a rather bad social reputation, especially traveling ones who often sold a sack (priced at about a day's wage) with lots of rubbish mixed in to farmers and townsfolk.
Historically the massive production of charcoal (at its height employing hundreds of thousands, mainly in Alpine and neighbouring forests) has been a major cause of deforestation, especially in Central Europe. In England, many woods were managed as coppices, which were cut and regrew cyclically, so that a steady supply of charcoal would be available (in principle) forever; complaints (as early as in Stuart England) about shortages may relate to the results of temporary over-exploitation or the impossibility of increasing production. The increasing scarcity of easily harvested wood was a major factor for the switch to the fossil fuel equivalents, mainly coal and brown coal for industrial use.
The modern process of carbonizing wood, either in small pieces or as sawdust in cast iron
retorts, is extensively practiced where wood is scarce, and also by reason of the recovery of valuable byproducts (wood spirit, pyroligneous acid, wood tar), which the process permits. The question of the temperature of the carbonization is important; according to J. Percy, wood becomes brown at 220°C, a deep brown-black after some time at 280°, and an easily powdered mass at 310°.[citation needed] Charcoal made at 300° is brown, soft and friable, and readily inflames at 380°; made at higher temperatures it is hard and brittle, and does not fire until heated to about 700°.
In Finland and Scandinavia, the charcoal was considered the by-product of wood tar production. The best tar came from pine, thus pinewoods were cut down for tar
pyrolysis. The residual charcoal was widely used as substitute for metallurgical
coke on blast furnaces for smelting. Tar production led to rapid deforestation: it has been estimated all Finnish forests are younger than 300 years by their age. The end of tar production in the end of the 19th century meant also rapid re-forestation.
One of the most important historical applications of wood charcoal was as a constituent of gunpowder. It was also used in metallurgical operations as a reducing agent, but its application has been diminished by the introduction of coke, anthracite smalls, etc. A limited quantity is made up into the form of drawing crayons; but the greatest amount is used as a fuel, which burns hotter and cleaner than wood. Charcoal is often used by blacksmiths, for cooking, and for other industrial applications.
A charcoal powered bus being "fired up" in post war Japan (late 1940's)
Historically, charcoal was used in great quantities for smelting iron in bloomeries and later blast furnaces and finery forges. This was replaced for this by coke during the Industrial Revolution. For this purpose, charcoal in England was measured in dozens (or loads) consisting of 12 sacks or shems or seams, each of 8 bushels.
Commercially, charcoal is often found in either lump, briquette or extruded forms:
- Lump charcoal is made directly from hardwood material and usually produces far less ash than briquettes.
- While some briquettes are made from a combination of charcoal (heat source), brown coal (heat source), mineral carbon (heat source), borax, sodium nitrate (ignition aid), limestone (uniform visual ashing), starch (binder), raw sawdust (ignition aid) and possibly additives like paraffin or lighter fluid to aid in lighting them, other "natural" briquettes are made solely from charcoal and a binder. The charcoal briquette was first invented by Henry Ford from wood and sawdust scraps from his automotive plant.[1]
- Extruded charcoal is made by extruding either raw ground wood or carbonized wood into logs without the use of a binder. The heat and pressure of the extruding process hold the charcoal together. If the extrusion is made from raw wood material, the extruded logs are then subsequently carbonized.
The characteristics of charcoal products (lump, briquette or extruded forms) vary widely from product to product. Thus it is a common misconception to stereotype any kind of charcoal, saying which burns hotter, etc.
Charcoal is sometimes used to power commercial road vehicles, usually buses - in countries where oil is scarce or completely unavailable. In the years immediately after the second world war, charcoal buses were in regular use in Japan and are still used today in North Korea. [1]
The porosity of activated charcoal accounts for its ability to readily adsorb gases and liquids; charcoal is often used to filter water or adsorb odors. Its pharmacological action depends on the same property; it adsorbs the gases of the stomach and intestines, and also liquids and solids (hence its use in the treatment of certain poisonings). Charcoal filters are used in some types of gas mask to remove poisonous gases from inhaled air. Wood charcoal also to some extent removes coloring material from solutions, but animal charcoal is generally more effective.
Animal charcoal or bone black is the carbonaceous residue obtained by the dry distillation of bones; it contains only about 10% carbon, the remainder being calcium and magnesium phosphates (80%) and other inorganic material originally present in the bones. It is generally manufactured from the residues obtained in the glue and gelatin industries. Its decolorizing power was applied in 1812 by Derosne to the clarification of the syrups obtained in sugar refining; but its use in this direction has now greatly diminished, owing to the introduction of more active and easily managed reagents. It is still used to some extent in laboratory practice. The decolorizing power is not permanent, becoming lost after using for some time; it may be revived, however, by washing and reheating.
Four sticks of vine charcoal and four sticks of compressed charcoal.
Charcoal is used in art for drawing, making rough sketches in painting, and is one of the possible media for making a parsemage. It must usually be preserved by the application of a fixative. Artists generally utilize charcoal in three forms:
- Vine charcoal is created by burning sticks of wood (usually willow or linden/Tilia) into soft, medium, and hard consistencies. Bamboo charcoal is the principal tool in Japanese Sumi-e (炭絵 lit: charcoal drawing) art.
- Compressed charcoal charcoal powder mixed with gum binder compressed into round or square sticks. The amount of binder determines the hardness of the stick. Compressed charcoal is used in charcoal pencils.
- Powdered charcoal is often used to "tone" or cover large sections of a drawing surface. Drawing over the toned areas will darken it further, but the artist can also lighten (or completely erase) within the toned area to create lighter tones.
One additional use of charcoal rediscovered recently is in horticulture. Although American
gardeners have been using charcoal for a short while, research on Terra preta
soils in the Amazon has found the widespread use of biochar by pre-Columbian natives to turn otherwise unproductive soil into very rich soil. The technique may find modern application, both to improve soils and as a means of carbon sequestration.
Sources, references and external links
- Ignite Products - New generation charcoal products.
- Barbecue Charcoal - The available choices for the backyard barbecue
- Natural History of Europe - 2005 TV co-production including BBC and ZDF
- On Charcoal
- The Valley - BBC TV - one year of life on a 17th century farm reenacted by archaeologists and historians
- The Lump Charcoal Database - Information about lump charcoal.
- H E Z Organisation - Information about charcoal in Germany.
- How charcoal briquettes are made.
- [2] - Information about charcoal.
- Photo of traditional charcoal production A forest kiln
- [3] - Charcoal making community for livelihood
- [4] - Traditional charcoal production method, India
- The River Wey and Wey Navigations Community Site — a non-commercial site of over 200,000 words all about the Wey Valley and includes a photo file on charcoal production and information relating to gunpowder manufacture at Chilworth.
- [5]
Catoctin Mountain Park, Maryland, USA, includes interpretive features ("Charcoal Trail", etc) on the history of charcoal making in the area. - Bamboo Charcoal - Properties and Facts
- Coconut Charcoal - Facts
- Simple Home Charcoal Process
Medical Encyclopedia:Charcoal, Activated
Definition
Activated charcoal is a fine, black, odorless, and tasteless powder. It is made from wood or other materials that have been exposed to very high temperatures in an airless environment. It is then treated, or activated, to increase its ability to adsorb by reheating with oxidizing gas or other chemicals to break it into a very fine powder. Activated charcoal is pure carbon specially processed to make it highly adsorbent of particles and gases in the body's digestive system.
Activated charcoal has often been used since ancient times to cure a variety of ailments including poisoning. Its healing effects have been well documented since as early as 1550 B.C. by the Egyptians. However, charcoal was almost forgotten until 15 years ago when it was rediscovered as a wonderful oral agent to treat most overdoses and toxins.
Description
Activated charcoal's most important use is for treatment of poisoning. It helps prevent the absorption of most poisons or drugs by the stomach and intestines. In addition to being used for most swallowed poisons in humans, charcoal has been effectively used in dogs, rabbits, rats, and other animals, as well. It can also adsorb gas in the bowels and has been used for the treatment of gas or diarrhea. Charcoal's other uses such as treatment of viruses, bacteria, bacterial toxic byproducts, snake venoms and other substances by adsorption have not been supported by clinical studies. By adding water to the powder to make a paste, activated charcoal can be used as an external application to alleviate pain and itching from bites and stings.
Poisons and drug overdoses
It is estimated that one million children accidentally overdose on drugs mistaken as candies or eat, drink, or inhale poisonous household products each year. Infants and toddlers are at the greatest risk for accidental poisoning. Activated charcoal is one of the agents most commonly used for these cases. It can absorb large amounts of poisons quickly. In addition, it is non-toxic, may be stored for a long time, and can be conveniently administered at home. Charcoal works by binding to irritating or toxic substances in the stomach and intestines. This prevents the toxic drug or chemical from spreading throughout the body. The activated charcoal with the toxic substance bound to it is then excreted in the stool without harm to the body. When poisoning is suspected the local poison control center should be contacted for instructions. They may recommend using activated charcoal, which should be available at home so that it can be given to the poisoned child or pet immediately. For severe poisoning, several doses of activated charcoal may be needed.
Intestinal disorders
In the past, activated charcoal was a popular remedy for gas. Even before the discovery of America by Europeans, Native Americans used powdered charcoal mixed with water to treat an upset stomach. Now charcoal is being rediscovered as an alternative treatment for this condition. Activated charcoal works like a sponge. Its huge surface area is ideal for soaking up different substances, including gas. In one study, people taking activated charcoal after eating a meal with high gas-producing foods did not produce more gas than those who did not have these foods. Charcoal has also been used to treat other intestinal disorders such as diarrhea, constipation, and cramps. There are few studies to support these uses and there are also concerns that frequent use of charcoal may decrease absorption of essential nutrients, especially in children.
Other uses
Besides being a general antidote for poisons or remedy for gas, activated charcoal has been used to treat other conditions as well. Based on its ability to adsorb or bind to other substances, charcoal has been effectively used to clean skin wounds and to adsorb waste materials from the gastrointestinal tract. In addition, it has been used to adsorb snake venoms, viruses, bacteria, and harmful materials excreted by bacteria or fungi. However, because of lack of scientific studies, these uses are not recommended. Activated charcoal, when used together with other remedies such as aloe vera, acidophilus, and psyllium, helps to keep symptoms of ulcerative colitis under control. While charcoal shows some anti-aging activity in rats, it is doubtful if it can do the same for humans.
Preparations
For Poisoning
Activated charcoal is available without prescription. However, in case of accidental poisoning or drug overdose an emergency poison control center, hospital emergency room, or doctor's office should be called for advice. In cases where both syrup of ipecac and charcoal are recommended for treatment of the poison, ipecac should be given first. Charcoal should not be given for at least 30 minutes after ipecac or until vomiting from ipecac stops. Activated charcoal is often mixed with a liquid before being swallowed or put into the tube leading to the stomach. Activated charcoal is available as 30-gram liquid bottles. It is also available in 15-gram container sizes and as slurry of charcoal pre-mixed in water or as a container in which water or soda pop is added. Keeping activated charcoal at home is a good idea so that it can be taken immediately when needed for treatment of poisoning.
For acute poisoning, the dosage is as follows:
- infants (under 1 year of age): 1 g/kg
- children (1-12 years of age): 15-30 g or 1-2 g/kg with at least 8 oz of water
- adults: 30-100 g or 1-2 g/kg with at least 8 oz of water
For Diarrhea or Gas
A person can take charcoal tablets or capsules with water or sprinkle the content onto foods. The dosage for treatment of gas or diarrhea in adults is 520-975 mg after each meal and up to 5 g per day.
Precautions
Parents should keep activated charcoal on hand in case of emergencies.
Charcoal should not be taken together with syrup of ipecac, as the charcoal will adsorb the ipecac. Charcoal should be taken 30 minutes after ipecac or after the vomiting from ipecac stops.
Some activated charcoal products contain sorbitol. Sorbitol is a sweetener as well as a laxative, therefore, it may cause severe diarrhea and vomiting. These products should not be used in infants.
Charcoal may interfere with the absorption of medications and nutrients such as vitamins or minerals. For uses other than for treatment of poisoning, charcoal should be taken two hours after other medications.
Charcoal should not be used to treat poisoning caused by corrosive products such as lye or other strong acids or petroleum products such as gasoline, kerosene, or cleaning fluids. Charcoal may make the condition worse and delay diagnosis and treatment. In addition, charcoal is also not effective if the poison is lithium, cyanide, iron, ethanol, or methanol.
Parents should not mix charcoal with chocolate syrup, sherbet, or ice cream, even though it may make charcoal taste better. These foods may prevent charcoal from working properly.
Activated charcoal may cause swelling or pain in the stomach. A doctor should be notified immediately. It has been known to cause problems in people with intestinal bleeding, blockage or those people who have had recent surgery. These patients should talk to their doctor before using this product.
Charcoal may be less effective in people with slow digestion.
Charcoal should not be given for more than three or four days for treatment of diarrhea. Continuing for longer periods may interfere with normal nutrition.
Charcoal should not be used in children under three years of age to treat diarrhea or gas.
Activated charcoal should be kept out of reach of children.
Side Effects
Charcoal may cause constipation when taken for overdose or accidental poisoning. A laxative should be taken after the crisis is over.
Activated charcoal may cause the stool to turn black. This is to be expected.
Pain or swelling of the stomach may occur. A doctor should be consulted.
Interactions
Activated charcoal should not be mixed together with chocolate syrup, ice cream or sherbet. These foods prevent charcoal from working properly.
Resources
Books
Blumenthal, Mark. Linden Charcoal. The Complete German Commission E Monographs, Therapeutic Guide to Herbal Medicines, American Botanical Council, Boston: Integrative Medicine Communications, 1998. Accessed online. http://home.mdconsult.com.
Cooney, David. Activated Charcoal: Antidote, Remedy, and Health Aid. Brushton, NY: TEACH Services, Inc., 1999.
Lacy Charles F., Lora L. Amstrong, Naomi B. Ingrim, and Leonard L. Lance. Charcoal. The Drug Information Handbook Pocket Version: 1998-1999, Hudson, OH: Lexi-Comp Inc., 1998.
Roberts. Activated Charcoal. Clinical Procedures in Emergency Medicine, Philadelphia, PA: W. B. Saunders Company, 1998: 726-8. Accessed online. http://home.mdconsult.com.
Wilson, Billie A., Margaret T. Shannon, and Carolyn L. Stang. Charcoal, Activated (Liquid Antidote). Nurses Drug Guide 2000, Stamford, CT: Appleton & Lange, 2000.
Periodicals
Bond, C. Randall. "Activated Charcoal in the Home: Helpful and Important or Simply a Distraction." Pediatrics (January 2002) : 145.
[Article by: Mai Tran; Teresa G. Odle]
— Mai Tran
Medical Encyclopedia:Charcoal, Activated
Definition
Activated charcoal is a fine, black, odorless, and tasteless powder. It is made from wood or other materials that have been exposed to very high temperatures in an airless environment. It is then treated, or activated, to increase its ability to adsorb by reheating with oxidizing gas or other chemicals to break it into a very fine powder. Activated charcoal is pure carbon specially processed to make it highly adsorbent of particles and gases in the body's digestive system.
Activated charcoal has often been used since ancient times to cure a variety of ailments including poisoning. Its healing effects have been well documented since as early as 1550 B.C. by the Egyptians. However, charcoal was almost forgotten until 15 years ago when it was rediscovered as a wonderful oral agent to treat most overdoses and toxins.
Description
Activated charcoal's most important use is for treatment of poisoning. It helps prevent the absorption of most poisons or drugs by the stomach and intestines. In addition to being used for most swallowed poisons in humans, charcoal has been effectively used in dogs, rabbits, rats, and other animals, as well. It can also adsorb gas in the bowels and has been used for the treatment of gas or diarrhea. Charcoal's other uses such as treatment of viruses, bacteria, bacterial toxic byproducts, snake venoms and other substances by adsorption have not been supported by clinical studies. By adding water to the powder to make a paste, activated charcoal can be used as an external application to alleviate pain and itching from bites and stings.
Poisons and drug overdoses
It is estimated that one million children accidentally overdose on drugs mistaken as candies or eat, drink, or inhale poisonous household products each year. Infants and toddlers are at the greatest risk for accidental poisoning. Activated charcoal is one of the agents most commonly used for these cases. It can absorb large amounts of poisons quickly. In addition, it is non-toxic, may be stored for a long time, and can be conveniently administered at home. Charcoal works by binding to irritating or toxic substances in the stomach and intestines. This prevents the toxic drug or chemical from spreading throughout the body. The activated charcoal with the toxic substance bound to it is then excreted in the stool without harm to the body. When poisoning is suspected the local poison control center should be contacted for instructions. They may recommend using activated charcoal, which should be available at home so that it can be given to the poisoned child or pet immediately. For severe poisoning, several doses of activated charcoal may be needed.
Intestinal disorders
In the past, activated charcoal was a popular remedy for gas. Even before the discovery of America by Europeans, Native Americans used powdered charcoal mixed with water to treat an upset stomach. Now charcoal is being rediscovered as an alternative treatment for this condition. Activated charcoal works like a sponge. Its huge surface area is ideal for soaking up different substances, including gas. In one study, people taking activated charcoal after eating a meal with high gas-producing foods did not produce more gas than those who did not have these foods. Charcoal has also been used to treat other intestinal disorders such as diarrhea, constipation, and cramps. There are few studies to support these uses and there are also concerns that frequent use of charcoal may decrease absorption of essential nutrients, especially in children.
Other uses
Besides being a general antidote for poisons or remedy for gas, activated charcoal has been used to treat other conditions as well. Based on its ability to adsorb or bind to other substances, charcoal has been effectively used to clean skin wounds and to adsorb waste materials from the gastrointestinal tract. In addition, it has been used to adsorb snake venoms, viruses, bacteria, and harmful materials excreted by bacteria or fungi. However, because of lack of scientific studies, these uses are not recommended. Activated charcoal, when used together with other remedies such as aloe vera, acidophilus, and psyllium, helps to keep symptoms of ulcerative colitis under control. While charcoal shows some anti-aging activity in rats, it is doubtful if it can do the same for humans.
— Mai Tran
Charcoal Briquette
http://www.enotes.com/how-products-encyclopedia/charcoal-briquette
Background
Charcoal is a desirable fuel because it produces a hot, long-lasting, virtually smokeless fire. Combined with other materials and formed into uniform chunks called briquettes, it is popularly used for outdoor cooking in the United States. According to the barbecue Industry Association, Americans bought 883,748 tons of charcoal briquettes in 1997.
Basic charcoal is produced by burning a carbon-rich material such as wood in a low-oxygen atmosphere. This process drives off the moisture and volatile gases that were present in the original fuel. The resulting charred material not only burns longer and more steadily than whole wood, but it is much lighter (one-fifth to one-third of its original weight).
History
Charcoal has been manufactured since pre-historic times. Around 5,300 years ago, a hapless traveler perished in the Tyrolean Alps. Recently, when his body was recovered from a glacier, scientists found that he had been carrying a small box containing bits of charred wood wrapped in maple leaves. The man had no fire-starting tools such as flint with him, so it appears that he may have carried smoldering charcoal instead.
As much as 6,000 years ago, charcoal was the preferred fuel for smelting copper. After the invention of the blast furnace around 1400 A.D., charcoal was used extensively throughout Europe for iron smelting. By the eighteenth century, forest depletion led to a preference for coke (a coal-based form of charcoal) as an alternative fuel.
Plentiful forests in the eastern United States made charcoal a popular fuel, particularly for blacksmithing. It was also used in the western United States through the late 1800s for extracting silver from ore, for railroad fueling, and for residential and commercial heating.
Charcoal's transition from a heating and industrial fuel to a recreational cooking material took place around 1920 when Henry Ford invented the charcoal briquette. Not only did Ford succeed in making profitable use of the sawdust and scrap wood generated in his automobile factory, but his sideline business also encouraged recreational use of cars for picnic outings. Barbecue grills and Ford Charcoal were sold at the company's automobile dealerships, some of which devoted half of their space to the cooking supplies business.
Historically, charcoal was produced by piling wood in a cone-shaped mound and covering it with dirt, turf, or ashes, leaving air intake holes around the bottom of the pile and a chimney port at the top. The wood was set afire and allowed to burn slowly; then the air holes were covered so the pile would cool slowly. In more modern times, the single-use charcoal pit was replaced by a stone, brick, or concrete kiln that would hold 25-75 cords of wood (1 cord = 4 ft x 4 ft x 8 ft). A large batch might burn for three to four weeks and take seven to 10 days to cool.
This method of charcoal production generates a significant amount of smoke. In fact, changes in the color of the smoke signal transitions to different stages of the process. Initially, its whitish hue indicates the presence of steam, as water vapors are driven out of the wood. As other wood components such as resins and sugars burn, the smoke becomes yellowish. Finally the smoke changes to a wispy blue, indicating that charring is complete; this is the appropriate time to smother the fire and let the kiln's contents cool.
An alternative method of producing charcoal was developed in the early 1900s by Orin Stafford, who then helped Henry Ford establish his briquette business. Called the retort method, this involves passing wood through a series of hearths or ovens. It is a continuous process wherein wood constantly enters one end of a furnace and charred material leaves the other; in contrast, the traditional kiln process burns wood in discrete batches. Virtually no visible smoke is emitted from a retort, because the constant level of output can effectively be treated with emission control devices such as afterburners.
Raw Materials
Charcoal briquettes are made of two primary ingredients (comprising about 90% of the final product) and several minor ones. One of the primary ingredients, known as char, is basically the traditional charcoal, as described above. It is responsible for the briquette's ability to light easily and to produce the desired wood-smoke flavor. The most desirable raw material for this component is hardwoods such as beech, birch, hard maple, hickory, and oak. Some manufacturers also use softwoods like pine, or other organic materials like fruit pits and nut shells.
The other primary ingredient, used to produce a high-temperature, long-lasting fire, is coal. Various types of coal may be used, ranging from sub-bituminous lignite to anthracite.
Minor ingredients include a binding agent (typically starch made from corn, milo, or wheat), an accelerant (such as nitrate), and an ash-whitening agent (such as lime) to let the backyard barbecuer know when the briquettes are ready to cook over.
The Manufacturing Process
The first step in the manufacturing process is to char the wood. Some manufacturers use the kiln (batch) method, while others use the retort (continuous) method.
Charring the wood
- 1 (Batch process) It takes a day or two to load a typical-size concrete kiln with about 50 cords of wood. When the fire is started, air intake ports and exhaust vents are fully open to draw in enough oxygen to produce a hot fire. During the week-long burning period, ports and vents are adjusted to maintain a temperature between about 840-950° F (450-510° C). At the end of the desired burning period, air intake ports are closed; exhaust vents are sealed an hour or two later, after smoking has stopped, to avoid pressure build-up within the kiln. Following a two-week cooling period, the kiln is emptied, and the carbonized wood(char) is pulverized.
- 2 (Continuous process) Wood is sized (broken into pieces of the proper dimension) in a hammer mill. A particle size of about 0.1 in (3 mm) is common, although the exact size depends on the type of wood being used (e.g., bark, dry sawdust, wet wood). The wood then passes through a large drum dryer that reduces its moisture content by about half (to approximately 25%). Next, it is fed into the top of the multiple-hearth furnace (retort).
Externally, the retort looks like a steel silo, 40-50 ft (12.2-15.2 m) tall and 20-30 ft (6.1-9.14 m) in diameter. Inside, it contains a stack of hearths(three to six, depending on the desired production capacity). The top chamber is the lowest-temperature hearth, on the order of 525° F (275° C), while the bottom chamber burns at about 1,200° F (650° C). External heat, from oil-or gas-fired burners, is needed only at the beginning and ending stages of the furnace; at the intermediate levels, the evolving wood gases burn and supply enough heat to maintain desired temperature levels.
Within each chamber, the wood is stirred by rabble arms extending out from a center shaft that runs vertically through the entire retort. This slow stirring process (1-2 rpm) ensures uniform combustion and moves the material through the retort. On alternate levels, the rabble arms push the burning wood either toward a hole around the central shaft or toward openings around the outer edge of the floor so the material can fall to the next lower level. As the smoldering char exits the final chamber, it is quenched with a cold-water spray. It may then be used immediately, or it may be stored in a silo until it is needed.
A typical retort can produce approximately 5,500 lb (2.5 metric tons) of char per hour.
Carbonizing the coal
- 3 Lower grades of coal may also be carbonized for use in charcoal. Crushed coal is first dried and then heated to about 1,100° F (590° C) to drive off the volatile components. After being air-cooled, it is stored until needed.
Briquetting
- 4 Charcoal, and minor ingredients such as the starch binder are fed in the proper proportions into a paddle mixer, where they are thoroughly blended. At this point, the material has about a 35% moisture content, giving it a consistency somewhat like damp topsoil.
- 5 The blended material is dropped into a press consisting of two opposing rollers containing briquette-sized indentations. Because of the moisture content, the binding agent, the temperature(about 105° F or 40° C), and the pressure from the rollers, the briquettes hold their shape as they drop out the bottom of the press.
- 6 The briquettes drop onto a conveyor, which carries them through a single-pass dryer that heats them to about 275° F (135° C) for three to four hours, reducing their moisture content to around 5%. Briquettes can be produced at a rate of 2,200-20,000 lb (1-9 metric tons) per hour. The briquettes are either bagged immediately or stored in silos to await the next scheduled packaging run.
Bagging
- 7 If "instant-light" briquettes are being produced, a hydrocarbon solvent is atomized and sprayed on the briquettes prior to bagging.
- 8 Charcoal briquettes are packaged in a variety of bag sizes, ranging from 4-24 lb. Some small, convenience packages are made so that the consumer can simply light fire to the entire bag without first removing the briquettes.
Byproducts/Waste
During the late nineteenth and early twentieth centuries, recovery of acetic acid and methanol as byproducts of the wood-charring process became so important that the charcoal itself essentially became the byproduct. After the development of more-efficient and less-costly techniques for synthesizing acetic acid and methanol, charcoal production declined significantly until it was revitalized by the development of briquettes for recreational cooking.
The batch process for charring wood produces significant amounts of particulateladen smoke. Fitting the exhaust vents with afterburners can reduce the emissions by as much as 85%, but because of the relatively high cost of the treatment, it is not commonly used.
Not only does the more constant level of operation of retorts make it easier to control their emissions with afterburners, but it allows for productive use of combustible off-gases. For example, these gases can be used to fuel wood dryers and briquette dryers, or to produce steam and electricity.
Charcoal briquette production is environmentally friendly in another way: the largest briquette manufacturer in the United States uses only waste products for its wood supply. Woodshavings, sawdust, and bark from pallet manufacturers, flooring manufacturers, and lumber mills are converted from piles of waste into useful briquettes.
The Future
Charcoal and briquette production methods have changed little in the past several decades. The most significant innovation in recent years has been the development of "instant-light" briquettes. A new version being introduced in 1998 will be ready to cook on in about 10 minutes.
Where to Learn More
Books
Emrich, Walter. Handbook of Charcoal Making: The Traditional and Industrial Methods. Hingham, MA: Kiuwer Academic Publishers, 1985.
Moscowitz, C. M. Source Assessment: Charcoal Manufacturing: State of the Art. Cincinnati, Ohio: Environmental Protection Agency, Office of Research and Development, Industrial Environmental Research Laboratory, 1978.
Periodicals
Scharabok, Ken. "Amaze Your Friends and Neighbors: Make Your Own Charcoal!" Countryside & Small Stock Journal (May 1997): 27-28.
Zeier, Charles D. "Historic Charcoal Production Near Eureka, Nevada: An Archaeological Perspective." Historical Archaeology 21(1987): 81-101.
—Loretta Hall
Minggu, 14 September 2008
Rencana Produksi Arang PT. CIPTAMAS BUMISUBUR
- bangsal yang mampu memuat 50 tungku sebanyak 5 bangsal
- tungku yang telah dan sedang berproduksi sebanyak 4 tungku, masing-masing dengan bahan baku50 ton kayu bakau dapat menghasilkan 12 ton arang/bulan
- diselesaikan sebanyak keseluruhan 50 tungku dan mengahasilkan setiap bulan 500 ton arang
- diselesaikan 100 tungku dengan produksi 1.000 ton arang bakau / bulan
Kamis, 11 September 2008
KETERSEDIAAN LAHAN HTI PT. CIPTAMAS BUMISUBUR
No | BLOK | Luas Lahan ( Ha ) | |||
Total Luas Lahan | Lahan tersedia | Lahan peruntukan lain | |||
1 | I Kabupaten Banyuasin | 6.000 Ha | 6.000 Ha | a. Zona Lindung | 17, 5 km |
2 | II Kabupaten Ogan Komering Ilir | 1.550 Ha | 1.550 Ha | a. Zona Lindung | 8,25 km |
J u m l a h | 7.550 Ha | 7.550 Ha | 25,75 km |
Sasaran Kegiatan Usaha Pemanfaatan Hasil Hutan Kayu HTI Dalam Hutan Tanaman
No | Faktor Intern | Satuan | Sasaran | Cara Pencapaian |
1 |
Tata Batas Areal Kerja dan Pemetaan |
km km lembar lembar lembar |
Penataan Batas : - Batas sendiri = ± 55 km - Batas persekutuan = Pemetaan : - Peta dasar = - Peta tata ruang = - Peta kerja = sesuai kebutuhan |
- Koordinasi dengan Badan Planologi Dephut - Inventarisasi kondisi Kawasan yang kemudian Dipetakan. - Pembuatan peta dengan GIS |
2 | Penataan Areal Kerja | ha ha ha | Tan.Pokok = 5.285 ha Kw.Lindung = 1.288 ha Sarana prasarana = 5 ha | Overlay berbagai kondisi kawasan yang kemudian menentukan peruntukan. |
3 | Inventarisasi Tegakan | ha/daur ha/daur ha/daur | 588 | Dilakukan dengan Intensitas Sampling 0,6-10% sesuai sasaran dan permasalahannya |
4 | Pembukaan wilayah Hutan | km km Unit Unit | Kanal besar = Kanal kecil = TPn = sesuai jumlah petak TPK = 1 | Pembuatan desain kanal sesuai dengan kelasnya. Pembuatan TPn dan TPK sesuai dengan kebutuhannya |
5 | Penyiapan Lahan | ha ha | Tanaman Pokok = 5.285 ha Tanaman pada areal bekas pemanenan = 5.285 ha | Dilaksanakan dengan system mekanis/non mekanis |
6 | Pembibitan | btg/th | Bibit tanaman pokok = 11.627.000 batang | Membuat areal persemaian permanent yang baik |
7 | Penanaman | ha/daur | Tanaman pokok = 5.285 ha | Dilaksanakan berdasarkan perencanaan yang dibuat. |
8 | Pemeliharaan | ha/daur | Tanaman pokok = 5.285 ha | Dilaksanakan berdasarkan perencanaan yang dibuat |
9 | Perlindungan dan Pengaman Hutan | ha | Gangguan keamanan kawasan meliputi seluruh areal | Identifikasi jenis gangguan. Membentuk satuan pengamanan hutan. Bekerjasama dengan masyarakat dalam penanganan gangguan kawasan |
10 | Penebangan /pemanenan | ha/daur m3/daur m3/thn | Luas : 5.285 ha Tanaman pokok = Bakau + Acacia Volume : 766.325 m3 | Penetapan RIL sebagai hal yang harus dilakukan |
11 | Pengolahan dan pemasaran hasil | m3/daur m3/thn | Tanaman pokok = 766.325 m3 | Kayu hasil panen akan diserap sebagai bahan baku arang |
12 | Pengorganisasian dan tenagakerja | Orang | 300 orang | Pembentukan Organisasi Pengembangan SDM |
13 | Pembinaan/ Pemberdayaan Masyarakat Desa Hutan | Desa
Kecamatan | 5 (lima) desa (Ds.Muara, Jalur 21, jalur 18, Jalur 15, Jalur 13. 1 (satu) kecamatan | Memberdayakan kemampuan Masyarakat dalam turut melestarikan hutan dan lingkungan desa hutan |
14 | Penelitian dan Pengembangan | Aspek Penelitian | 7 aspek (tanah, silvikultur, perlindungan tanaman, pengembangan tegakan, manajemen tegakan, social ekonomi dan pasar) | Membentuk bagian Litbang Menjalin kerjasama dengan Instansi terkait dan perusahaan lainnya. |
15 | Pendidikan dan Pelatihan | Orang | 20 | Mengirim ke pelatihan di luar perusahaan dan in house training. |
16 | Pengadaan Sarana Dan Prasarana | 4 Unit 6 Unit 2 Unit 6 Unit 1 Unit | Base Camp dan sarana lainnya Pembuatan Tungku Peralatan kerja/berat Kendaraan darat/air Lain-lain | Realisasi sesuai dengan rencana investasi |
17 | Pengelolaan dan Pemantauan lingkungan | Ha Ha Ha Ha | Kawasan lindung pantai Areal efektif unit produksi Tanaman Pokok Tanaman Kehidupan | Mendasarkan pada kajian AMDAL (RKL-RPL) Hasil evaluasi pengelolaan dan pemantauan lingkungan |
18 | Monitoring dan Evaluasi | Kawasan lindung = 1.288 ha Areal efektif = Tanaman Pokok = 5.285 ha Tan. Kehidupan = 378 ha | Menetapkan Bagian Satuan Pengawas Internal (SPI) sebagai Lembaga yang melakukan monitoring. Menggunakan hasil kajian Litbang sebagai bahan pembuatan evaluasi. |
Foto hutan tanaman Agustus 2008
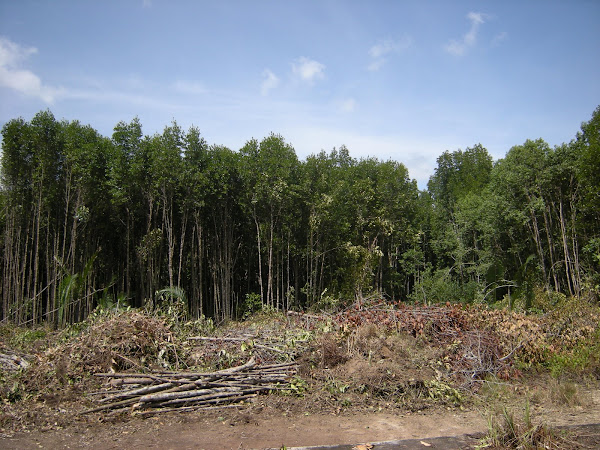
lahan yang dibersihkan untuk pembangunan tungku pembuatan arang, di latar belakang hutan tanaman yang sangat rapat dengan diameter 10-15 cm